“ A streamlined, high-performance bottle bottom for original 100% rPET bottles “: that's how Sidel sums up its new StarLITE®-R Premium solution, suitable for liquid dairy products, flavored water as well as juices, nectars, soft drinks, isotonic drinks and teas.
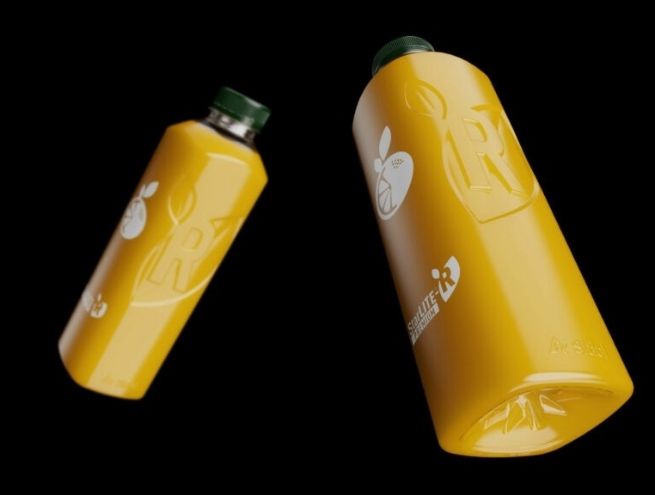
A refined and pure design
Guaranteed high production rates
Innovation isn't just about design. ‘High-end bottles are generally heavier than standard designs to ensure an excellent drinking experience thanks to the bottle's rigidity and preserved beverage quality. When bottles have an increased PET thickness, their bottoms are subject to deformation, especially if they are produced at high speed. (...) The technical features of Sidel's StarLITE®-R Premium make it possible to blow a 100% rPET bottle at high speed, while providing important guarantees: maximum bottom performance, superior bottle quality and visually appealing styling’ explains Sidel, pointing out that the design relies on the company's patented arching technology to prevent the flutes from being visible on the bottle's bottom and to optimize its geometry.
‘Composed of a high central arch and surrounded by lower edges with alternating widths and lengths, the bottom of the bottle is easy to blow out, with the guarantee of perfect material distribution and high bottom clearance. The bottom ensures bottle stability thanks to its wide surface. What's more, the bottom of the mold incorporates an improved cooling circuit that effectively cools the bottom of the bottle, particularly with rPET, which is processed at higher temperatures than virgin PET. (...) With these technical features, the production of the bottom of the bottle is highly efficient at high output (up to 2,500 bottles per hour per mold), thanks to the optimized geometry of the bottle design’ completes Sidel.
Sustainable solution
Sidel also highlights the low environmental impact of its new solution, compared with premium offerings already on the market. ‘Premium bottles are generally considered less sustainable than standard versions, as they use more PET material to offer increased shell thickness and they require higher blowing pressure. However, as global packaging regulations become increasingly focused on environmental impact, manufacturers are now looking for alternative solutions that deliver carbon savings. This is precisely what the StarLITE®-R Premium solution offers’ explains Pierrick Protais.
StarLITE®-R Premium can in fact be produced with 100% rPET, and Sidel has adapted its bottom-molding technology to the material to ensure a superior-quality bottle. Similarly, this easy-to-form base requires lower blowing pressure.
Sidel thus promises significant carbon dioxide savings for users of StarLITE®-R Premium bottle bottoms. ‘By switching from virgin PET to 100% rPET, manufacturers can save up to 3,100 tonnes of carbon dioxide equivalent per year. By reducing blow-molding pressure by up to 25% compared with the average premium bottle on the market, it is possible to save up to 61 tonnes of carbon dioxide equivalent per year’ summarizes Sidel.
The new high-end bottle base is designed for bottle sizes ranging from 0.25 liter to 2 liters, with the possibility of reaching up to 2,500 bottles per hour per mold.
Credits: Sidel’s website